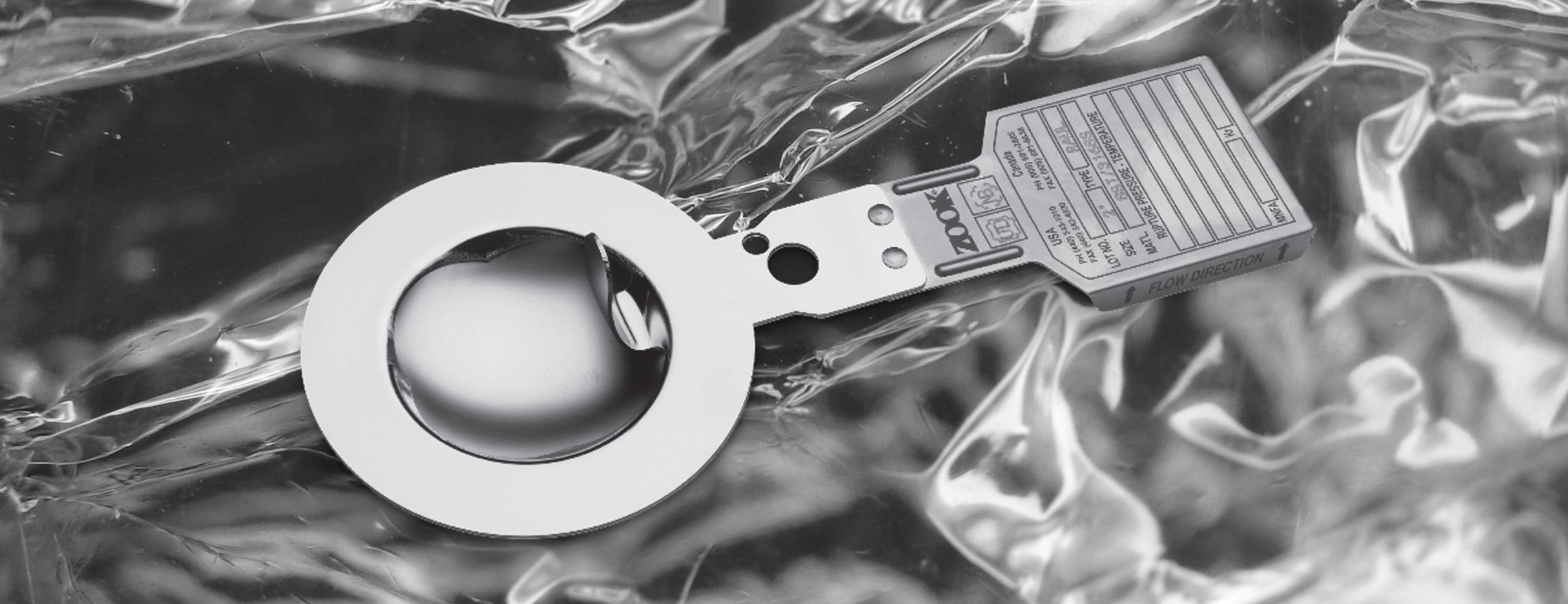
Corrosion des disques de rupture : minimisez les risques grâce aux revêtements
Les disques de rupture en métal sont fabriqués à partir de feuillards métalliques fins. Ils ne disposent d’aucune marge de corrosion dans leur conception. Lorsqu’ils sont exposés à des environnements corrosifs, leurs composants métalliques peuvent rapidement se détériorer.
Il est donc crucial de choisir un matériau compatible avec le fluide du procédé pour éviter toute détérioration. Cependant, lorsque des mesures de protection supplémentaires sont nécessaires, les revêtements pour disques de rupture offrent une protection efficace contre les agressions chimiques.
QUELLE EST LA DIFFÉRENCE ENTRE UNE MEMBRANE ET UN REVÊTEMENT ?
Une membrane (ou liner) est une couche de matériau ajoutée au disque de rupture. Elle recouvre soit la face en contact avec le fluide, soit la face d’évacuation. Son rôle est de créer une barrière protectrice contre la corrosion, les attaques chimiques et toute autre forme de dégradation susceptible d’altérer les performances du disque.
Un revêtement (ou coating) est une pellicule protectrice appliquée directement sur la surface du disque. Contrairement à une membrane, il ne peut pas être retiré car il est adhérent au disque. Ce traitement modifie donc les propriétés de surface et améliore la résistance chimique. Il réduit également les frottements et empêche l’adhésion du fluide.
Bien que leur objectif soit similaire, membranes et revêtements diffèrent par leur mode d’application et leur efficacité selon les conditions d’utilisation.
De manière générale, les membranes offrent de meilleures performances, une fiabilité accrue et une durée de vie plus longue que les revêtements pour plusieurs raisons :
- Performance et épaisseur :
Plus un revêtement est épais, moins il adhère efficacement au disque, ce qui peut compromettre sa tenue dans le temps. À l’inverse, une membrane, de par son épaisseur et sa conception, assure une protection plus durable contre la corrosion.
- Résistance aux dommages :
Les revêtements doivent adhérer parfaitement à la surface du disque. Toute irrégularité, choc ou contrainte mécanique peut nuire à l’adhérence et compromettre leur efficacité. Plus épaisses, les membranes résistent mieux aux agressions extérieures.
- Qualité et durabilité :
L’application des revêtements se fait manuellement. Leur homogénéité n’est donc pas toujours garantie. Les membranes, en revanche, offrent une protection plus uniforme et durable.
Les différents types de membranes pour disques de rupture : Choisir la meilleure solution
Notre fabricant ZOOK propose une large gamme de membranes adaptées à divers environnements. Le choix dépend de la résistance à la corrosion, de la température et de la pression de service. Une sélection adaptée optimise la durée de vie et l’efficacité du disque de rupture.
- PTFE (Polytétrafluoroéthylène) :
Commercialisé sous le nom de Teflon®, ce polymère fluoré est apprécié pour ses propriétés inertes et antiadhésives. Il est utilisé pour le revêtement de cuves, tuyauteries, pompes, vannes et joints, à des températures allant jusqu’à 260°C. Toutefois, son usage est limité aux joints, car il est sujet au fluage et perméable à certaines molécules.
- FEP (Éthylène-propylène fluoré) :
Alternative plus abordable au PTFE, il en conserve les principales qualités, mais sa température d’utilisation maximale est de 204°C.
- PFA (Perfluoroalkoxy) :
Ce copolymère fluoré (copolymère de TFE et de perfluorovinylméthyléther) est ignifuge et résiste à des températures jusqu’à 260°C. Ses propriétés antiadhésives en font un excellent choix pour les disques de rupture.
- PVDF (Polyfluorure de vinylidène) :
Connu sous le nom de Kynar®, ce polymère fluoré partiel offre une meilleure résistance mécanique que le PTFE. Sa température de service maximale est de 121°C. Cependant, sauf exceptions, il ne peut pas égaler les performances du film PTFE/PFA. Sa faible formabilité le destine uniquement aux disques plats.
CONCLUSION
Opter pour une membrane adaptée aux disques de rupture métalliques est un facteur clé pour assurer leur fiabilité et leur longévité, notamment dans des environnements corrosifs. Chaque matériau (PTFE, PFA, FEP, PVDF) présente des caractéristiques propres en termes de résistance chimique et thermique. Comprendre ces différences et les adapter aux besoins spécifiques de votre procédé permet non seulement de protéger le disque, mais aussi de réduire les temps d’arrêt et d’optimiser la sécurité de votre installation.
Besoin d’aide pour choisir la membrane idéale ? Contactez-nous par mail : contact@becep.net